
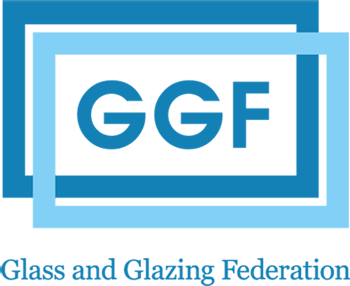
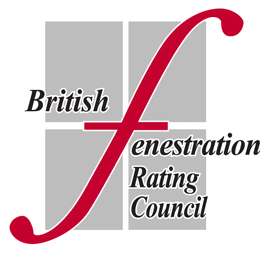
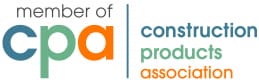
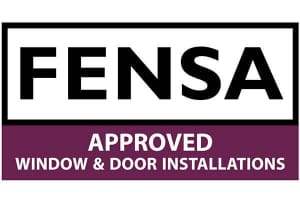
QUICK LINKS
GET IN TOUCH
- Steel Window Association, 7 Bell Yard, London. WC2A 2JR
- info@steel-window-association.co.uk
- 020 3475 8049
Plans are already underway, and the Steel Window Association is delighted to announce that that Awards will run in 2026 as it showcases impressive and remarkable projects as well as highlighting the expertise and knowledge that goes into creating beautiful steel work within the windows and doors sector.
The 2026 awards will consist of three judged categories: Domestic Project of the Year, Commercial Project of the Year & Refurbishment Project of the Year
The Supplier of the Year award will be voted for by the members
Our members will nominate the suppliers that provide high-quality goods and services that assist them in delivering award-winning projects.
We are pleased to have John Ramshaw, Technical Editor of Architecture Today onboard to judge the award entries next year and will present the awards to the winning members at County Hall in June 2026.
We are busy working on 2026 and will update this information as soon as the dates have been confirmed. But for now, let’s enjoy the 2025 winning projects.